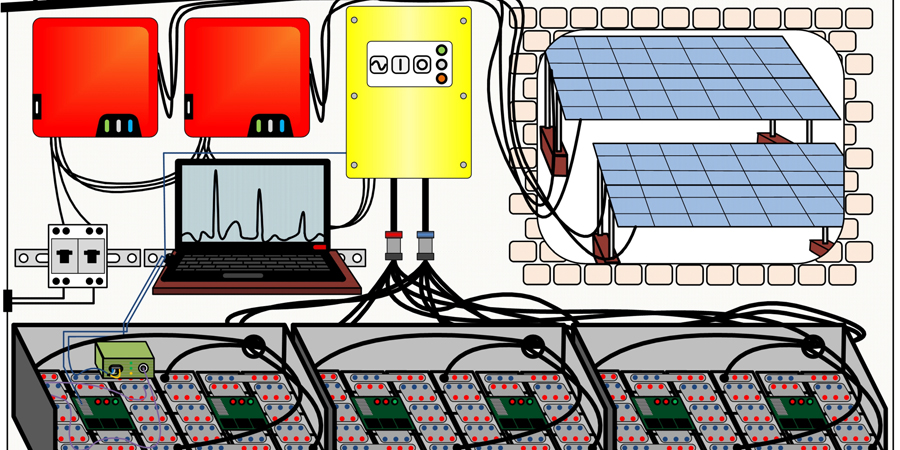
The future of lithium-ion batteries: Chinese hamburger ?
Judging from the structure of the lithium-ion battery, it is just like a common Chinese delicacy-Rou Jia Mo. The positive electrode and the negative electrode are like a steamed bun with two flaps torn apart, and the electrolyte sandwiched in between is meat; and the liquid electrolyte commonly used in lithium-ion batteries is exactly the same as the steamed steamed bun with wax sauce. Just as diners are picky about the amount of meat and the taste of the bun, people today have higher and higher requirements for battery capacity, safety and service life. How can we effectively increase the capacity of lithium-ion batteries? This is no different from the method of improving the quality of food. The selection of ingredients and the improvement of cooking skills are equally important. Positive electrode, negative electrode, electrolyte…Every part of the battery has room for improvement, and new materials are emerging in endlessly. Will the future lithium battery be the same as Roujiamo?
In 1973, British chemist Whittingham used a layered structure of titanium disulfide as a positive electrode and lithium metal as a negative electrode to assemble a battery, which opened the curtain on the development of contemporary lithium batteries. The widespread commercial use of modern lithium-ion batteries also benefited from Akira Yoshino’s application of graphite layered materials to the negative electrode. The three scientists awarded by the Nobel Prize in Chemistry in 2019: Whittingham, Goodenough and Akira Yoshino. The direct reason for the award is that they invented various layered, spinel and other positive and negative materials, which effectively promoted the success of lithium-ion batteries. .
Today’s lithium-ion batteries adopt a meat sandwich structure: the positive electrode and the negative electrode are similar to two sliced buns, and the “meat” in the middle is an electrolyte that conducts lithium ions and a diaphragm that blocks electrons. The energy that a lithium ion battery can store is mainly determined by the amount of lithium ions that can be stored in the positive electrode material and the negative electrode material.
As shown in Figure 1, the negative electrode currently mainly uses layered carbon materials such as petroleum coke , while the positive electrode uses layered metal salt materials . Lithium ions need to be embedded in the layered material for storage. The layered support material will occupy a large amount of the battery. The mass and volume of the battery cause low energy density of the battery. Lithium ion can be thought of as a worker in a building, and the reinforced concrete skeleton is similar to the layered support material in the positive/negative electrode. Although the reinforced concrete occupies most of the space and weight of the entire building, it can really contribute to the company. Those are the small hitters. Moreover, the larger the space occupied by each worker, the fewer people can be installed in the building. If the efficiency of each worker is the same, the lower the company’s overall profitability will be.
Cathode materials for lithium-ion batteries
Although the lithium-ion battery is good, its limited capacity and slow charging speed have contradicted the increasing battery capacity and power demand of the people. The current mainstream lithium-ion battery has an energy density of about 300 Wh/kg, which means that only 3.3 kg of lithium-ion batteries can carry one kilowatt-hour of electricity. In contrast, the energy density of gasoline is about 13000 Wh/kg, which is more than 40 times that of lithium-ion batteries. Even considering the thermal efficiency of automobile internal combustion engines of less than 40%, the current battery life of electric vehicles is still far behind that of fuel vehicles. .
Reducing costs, increasing safety, and increasing capacity are the main goals of the commercial development of cathode materials in recent years. As mentioned earlier, the cathode material can be regarded as a building equipped with lithium ions. Only lithium ions can store energy, while the layered frame material only provides support. Therefore, from the perspective of reducing costs, on the one hand, the expensive layered frame can be replaced with low-cost materials, just like changing a pure marble house to concrete construction; on the other hand, you can consider placing it in a unit volume of materials More lithium ion is like changing the original independent office into a grid room.
Among the cathode raw materials, the price of cobalt is higher and the capacity is lower. Therefore, cathode materials based on manganese and nickel oxides with lower cost and larger capacity have been gradually developed. For example, the ternary cathode material (NCM) that consumers are familiar with is a kind of lithium salt (LiNi 1-xy Co x Mn y O 2 ) composed of nickel, cobalt, and manganese oxides. The effect of more lithium ions. However, the ternary electrode material has frequent accidents in recent years, and the safety problem has been criticized. The reason is that nickel is prone to change in valence when the battery is charged, thereby depositing oxygen atoms, and the strong oxidizing oxygen atoms react violently with the organic electrolyte to cause the battery to burn. /explosion. (For the reason of lithium battery explosion, please refer to ” Why did the electric car explode? Uncover the secret of the explosion of lithium battery “)
If safety is the primary starting point, the most mature and reliable cathode material is lithium iron phosphate. Lithium iron phosphate changed the large flat structure of the original building and adopted a special olivine structure. The olivine structure can be compared to adding additional structural support in a large flat layer, thereby placing lithium ions in independent “single rooms”. Since each single room has sufficient support around it, it is ensured that the battery is not prone to floor collapse during use, and the safety of the battery is greatly improved. But the ensuing trouble is that because the lithium ion “lays flat”, the living environment is too “comfortable”, the lithium ion insertion-extraction process has high resistance and the battery power is low. Especially in a low temperature environment, the speed of lithium in and out is extremely slow, and the battery capacity may even decay to less than 50%, which is extremely unfriendly to use in cold areas. In addition, the single-cell structure further reduces the energy density of the battery. The molecular weight of the iron phosphate frame (FePO 4 ) is 150.8 g/mol, and the lithium ion is only 7 g/mol, that is , only 4% of the weight of the lithium iron phosphate can be The battery provides the capacity of lithium ion, and most of the weight is taken up by the supporting iron phosphate.
As mentioned earlier, if the idea of ”intercalating lithium ions into the interlayer/grid” is not abandoned, it is difficult to achieve a breakthrough increase in the capacity of the cathode material. In recent years, cathode materials based on the chemical reaction of lithium have been gradually proposed, and the typical representative is sulfur (S). Unlike lithium salt, sulfur can form a compound Li 2 S with lithium , which means that each sulfur atom with an atomic weight of 32 can be combined with two lithium ions. Compared with the existing metal lithium salt, the capacity can be directly increased by 10 Times, it is regarded as a promising next-generation cathode material. At present, relevant small-scale commercial products have begun to appear at home and abroad, and it is believed that they will gradually replace layered lithium salt materials into the consumer field in the near future.
Anode materials for lithium-ion batteries
Let’s take a look at the negative electrode material. The negative electrode is the key to the safety of lithium-ion batteries.
People who have experienced the age of nickel-metal hydride batteries in the early years should be familiar with the term “memory effect”. The memory effect means that if the battery is not fully charged and discharged, only the part of the last cycle can be used in the next charge and discharge, as if the previous experience has been remembered. Therefore, in the early days of using lithium batteries, many users habitually recharged the battery at 0%, and then unplugged the battery after it was fully charged. Unfortunately, this kind of operation will reduce the life of the lithium-ion battery, and it is more likely to cause battery failure or safety issues. why?
Currently used lithium-ion battery negative electrode materials are mostly based on layered carbon materials such as graphite. The principle is similar to that of positive electrode materials, in which lithium ions are inserted between graphite layers for storage. Lithium ions leave the graphite layers when discharging, and return between the graphite layers when charging. However, graphite is different from the lithium salt of the positive electrode material, and its layer-to-layer bonding ability is relatively weak, and it is easy to peel off layer by layer during charge and discharge. Fortunately, on the side where the graphite is close to the electrolyte, a protective film called the “solid electrolyte layer” (SEI layer) is formed several cycles in the early stages of the battery life. This protective film is only nanometer thick, but it has strong toughness and complex composition. It is mainly produced by the chemical reaction between organic electrolyte and lithium ions on the graphite surface. This SEI layer can lock the graphite and prevent layer-by-layer peeling.
In the actual use of the battery, if the battery is over-discharged, that is, when the lithium ions in the graphite layer have been exhausted, continue to ask for lithium ions from the graphite layer, the lithium ions in the SEI layer have to leave the electrode, causing the SEI layer to be destroyed; Similarly, if the battery is overcharged, because the space between the graphite layers is already occupied, the new lithium ions cannot be inserted, and can only be deposited on the graphite surface to form lithium metal, which will produce lithium dendrites, pierce the SEI layer, and cause SEI The layer is destroyed. Therefore, from the perspective of battery safety and health, it is recommended that users use lithium-ion battery equipment as soon as they use it, and do not have to wait until the battery is exhausted or must be fully charged.
In terms of capacity, it is similar to the layered material of the positive electrode. Since lithium ions are stored in carbon materials such as graphite based on the principle of insertion-extraction, a large amount of mass and space are occupied by graphite that does not provide capacity. It is imperative to develop new negative electrode materials. .
At present, the reserve army of next-generation anode materials is sufficient: Graphene is a kind of the next-generation anode material that is often mentioned. Graphene is a single-layer graphite. Compared with lithium ions that need to be embedded between two graphite layers in graphite, graphene can use a single-layer structure to directly insert lithium ions, so the capacity is directly doubled. In addition, materials such as silicon and tin can chemically react with lithium ions to form substances such as Li 4 Si and Li 4 Sn, which have greater capacity potential and are currently an important research hotspot for anodes.
Scientists are even more concerned about the lithium metal negative electrode that was once abandoned due to safety issues. The storage of lithium in the lithium metal negative electrode no longer relies on the insertion and extraction of lithium ions in the layered material, but directly reduces the lithium ions to simple substances for storage, so 100% of the weight and volume of the negative electrode can provide capacity, which is the most efficient The anode material. In fact, the earliest lithium-ion batteries used lithium metal directly as the negative electrode, but as shown in Figure 4, uneven deposition occurs during the cycle, forming a lithium metal “tip”, and a stronger electric field is formed around the tip, which promotes follow-up Lithium ions accelerate deposition at the tip. As a result, a large number of sharp and fractal lithium dendrites will continue to form, eventually piercing the battery diaphragm, causing a short circuit inside the battery, causing battery failure and even safety accidents.
The success of lithium metal anodes depends largely on the development of solid electrolytes.
Solid electrolyte
Remember the Roujiamo model of the lithium-ion battery we mentioned earlier? Whether it is a bun, a sandwich or a burger, the key to its taste comes from the sauce added at the end. The sauce organically blends the flavors of the steamed bun with the meat, realizing the double sublimation of the texture and taste of the steamed bun. It is delicious, but with a little regret. If the sauce overflows the Roujiabu system accidentally, it will cause the biggest safety crisis in the process of eating the Roujiabu-the clothes are soiled. The same goes for lithium-ion batteries.
Almost all currently commercialized lithium batteries use liquid electrolytes (gel electrolytes), which are composed of liquid organic solvents (sauce) and lithium salts (meat) dissolved in solvents. The reason for using a liquid electrolyte is that lithium ions must migrate between the positive and negative electrodes to store/release energy, while lithium is active in nature, and liquid organic solvents are required to ensure safe operation and efficient transmission. However, the flammable organic electrolyte itself brings a huge safety risk to the lithium-ion battery, especially when metal lithium is used as the negative electrode, the growth of lithium dendrites can easily cause internal short circuits in the battery, and the thermal runaway caused will cause the volatilization of the organic electrolyte. And burning. Therefore, the development of a solid electrolyte that can conduct lithium ions can not only avoid the use of flammable substances inside the battery, but also because the solid electrolyte is relatively strong, it can effectively inhibit the growth of lithium dendrites.
But this is difficult, even more difficult than getting people to accept the meat tongs without the sauce.
The primary difficulty is that the lithium ion migration rate in the solid is difficult to meet the demand . The fish can swim happily in the water, but it is difficult to move in the ice, and it will eventually become a dead fish. The same is true for lithium ion. Lithium ions can move quickly in a liquid electrolyte, but it is very difficult to move in a solid. The difficulty of lithium ion migration means that the internal resistance of the battery increases and the battery power decreases: Imagine that you are willing to accept a charge for 2 hours and only be able to talk for 5 minutes?
Another difficulty is that even if a solid electrolyte is used, since the solid electrolyte itself is a rigid material, the growth of lithium dendrites will still pierce the solid electrolyte, causing the electrolyte to crack and causing battery damage .
In order to solve this problem, scientists went the other way and proposed the idea of using a soft layer sandwich. “If the solid electrolyte is too rigid, then make him a soft sandwich.” Recently, a paper by Li Xin’s team at Harvard University in Nature gave a shot of a cardiotonic injection to solid electrolytes. In order to inhibit the growth of lithium dendrites, they designed a solid electrolyte with a five-layer luxurious Hamburg structure: graphite-LPSCI-LGPS-LPSCI-graphite. Graphite is similar to the bread of Hamburg, LPSCl, which is a compound composed of lithium phosphorus, sulfur and chlorine, Li 5.5 PS 4.5 Cl 1.5 , which is a relatively rigid (so easy to be pierced) solid electrolyte; LGPS, which is a compound composed of lithium germanium, phosphorus and sulfur Li 10 GeP 2 S 12 is a relatively unstable (soft and tough) solid electrolyte. The author believes that when the grown lithium dendrites pierce the rigid LPSCI layer, under the compression of the LPSCL and the dendrite penetration stress, the LGPS layer will decompose the germanium element to fill the cracks and prevent the electrolyte layer from being completely destroyed. At the same time, thanks to the solid electrolyte that can effectively prevent the layer of positive electrode material from peeling off, this structure can ensure that the battery still has 82% of the initial capacity after 10,000 cycles.
This self-healing strategy is very soft and overpowering. Compared with the strategy of blindly increasing the solid electrolyte modulus and preventing lithium dendrites from piercing, it may accelerate the research and development of solid electrolytes. But thinking about it from another angle, is it the only way to improve the safety by forcing the meat folder without sauce and sacrificing the taste to avoid safety problems? The answer to the question has yet to be tried by the “gourmet” of science and engineering. After all, the juicy biscuits with meat and donkey meat are also delicious!